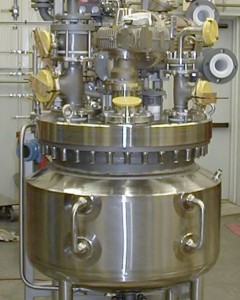
Reactor Flow-Pressure Control
Bronkhorst has developed a specialised combination of electronic pressure and thermal mass flow controllers for automated pressure control of reactor vessels.
This standard solution can be applied for low flow lab reactor systems as well as for high flow industrial applications as for instance in hydrogenation processes in the food and pharma industry at either low or (very) high pressure (up to 700 bar).
To optimize a chemical reaction, chemists must find the best combination of compounds and introduce these in precise proportions into the reaction chamber. This reactor may be kept at a certain pressure and temperature and a catalyst may be added to accelerate the reaction. The input of the reaction gases must be accurately measured at all times, also while pressurizing the reactor. An overshoot in flow (outside the scale of the mass flow meter) should be avoided, because this will introduce inaccuracy
Important topics essential to the success of the application include :
– Accurate measurement of gases
– Reaction and process pressure
– Programmable pressure profile
– Batch control
The standard configuration may slightly vary per application as many options are available. Furthermore, the instruments used may be in laboratory style or with rugged industrial housing, with protection to IP65 and with ATEX Zone 2 approval.
To illustrate the solution uniquely offered by Bronkhorst please see the schematic above.
At the inlet of the reactor, a Mass Flow Controller (MFC) provides the process gas delivery, whilst an Electronic Pressure Transmitter (EPT) measures the reactor pressure. At the outlet of the system there is a flow restriction which could simply be a (needle) valve or, as shown in the illustration, a Mass Flow Regulator (MFR) with local display.
The reactor pressure is controlled by giving a setpoint to the pressure transmitter. In the illustration this is achieved by a script programmed into a PC and delivered via RS232.
The integrated PID-controller of this pressure meter (Master) controls the valve position of the MFCs control valve (Slave). When building up the pressure in the reactor, the maximum inlet flow is restricted by the MFC, thus preventing a flow peak. By using the slave factor option, the maximum flow can be adjusted.
When the process pressure has reached the desired value, it is kept constant whilst the required amount of reaction gas is controlled with a constant flow. It is also possible to pre-set the total amount of reaction gas allowed into the system by using a batch control function Once the total amount is reached, the set-point for the MFC can be programmed to be reset to zero, thus switching off the gas supply, independent of the process pressure.
The scripted programme is available as part of the Freeware package of software tools available from Bronkhorst. Another important feature within this suite of programmes is the ability to send the measured data, and multiple parameters, directly to a spread-sheet or to a unique file. This eliminates the need for an operator to manually record such data.
In summary, simple straight forward pressure control solutions are available for a great many applications across the process industry. These tried and tested solutions are built upon technical expertise, knowledge and experience. Commonly a standardized solution is already available, however, with the great many options available it is possible to design bespoke assemblies to meet the requirements of virtually every need.
Download application note